back
The Costly Impact of Substandard Materials in Construction
Posted by Tristan Angelini on 30 April 2024
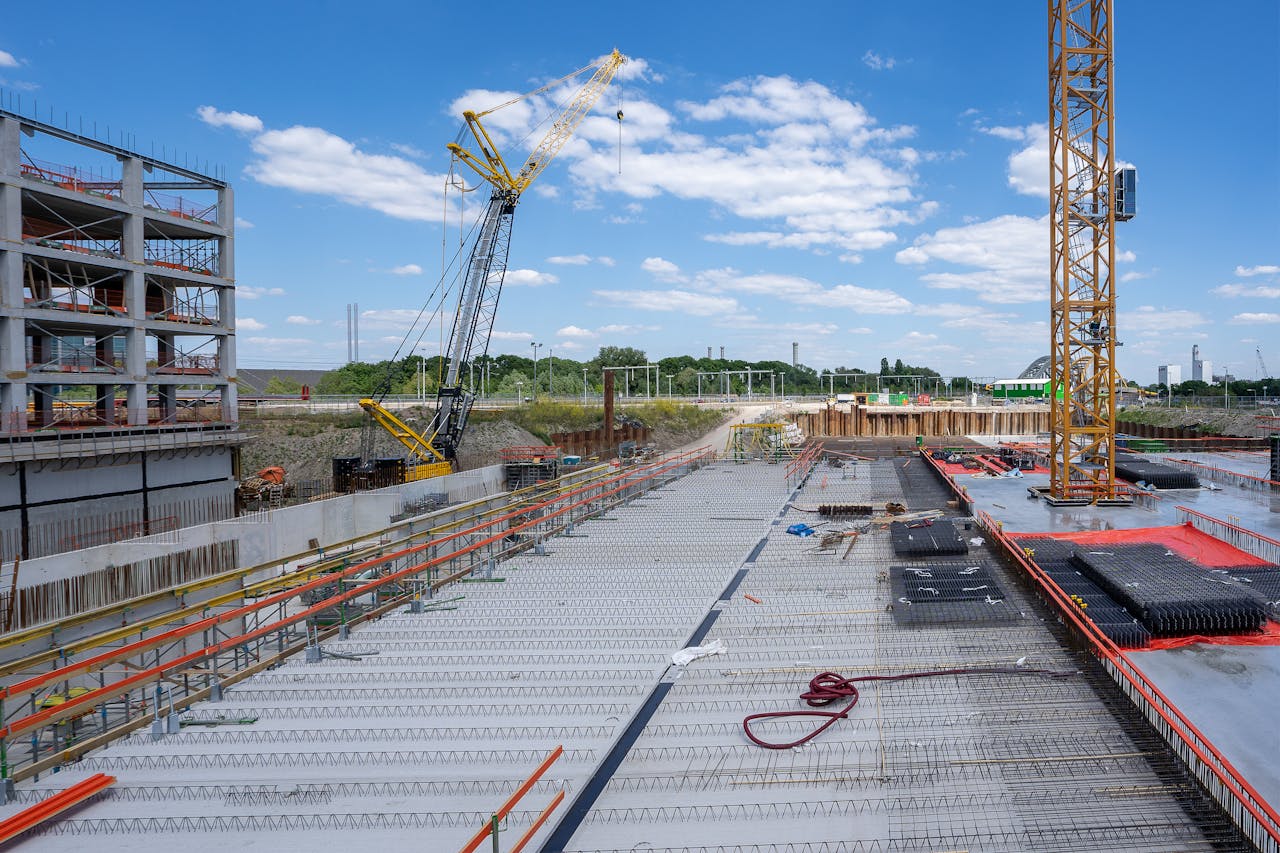
In the world of construction, every brick laid, every beam installed, and every nail driven is a building block for the future. However, when substandard materials are introduced into this equation, the consequences can reverberate far beyond the construction site, impacting safety, longevity, and the financial bottom line. In this blog, we delve into the detrimental effects of using substandard materials in construction and why prioritizing quality is paramount.
Safety Compromised
One of the most immediate and critical impacts of substandard materials in construction is compromised safety. Inferior materials may lack the strength, durability, or fire resistance necessary to uphold structural integrity, putting lives at risk. Whether it's a poorly manufactured steel beam prone to bending or a subpar concrete mix vulnerable to crumbling under pressure, the consequences of structural failure can be catastrophic.
Shortened Lifespan
Quality materials are the cornerstone of a durable and long-lasting structure. However, when substandard materials are utilized, the lifespan of the construction project is significantly shortened. From corroding pipes to deteriorating foundations, the use of inferior materials accelerates wear and tear, leading to costly repairs and replacements down the line. What might initially seem like a cost-saving measure can quickly turn into a financial burden as maintenance expenses escalate.
Economic Fallout
The financial ramifications of using substandard materials extend beyond immediate construction costs. Projects plagued by material deficiencies often incur additional expenses related to repairs, legal disputes, and diminished property values. Furthermore, the reputational damage inflicted on construction firms involved in such projects can result in lost contracts and tarnished credibility, further exacerbating the economic fallout.
Environmental Consequences
Construction activities already exert a significant environmental footprint, and the use of substandard materials only amplifies these effects. Cheaply manufactured materials may contain harmful chemicals or lack proper sustainability certifications, contributing to pollution and resource depletion. Additionally, the premature replacement of structures due to material degradation further exacerbates environmental degradation by increasing waste generation.
Regulatory Compliance
Building codes and regulations are designed to ensure the safety and quality of constructed facilities. However, the use of substandard materials can lead to non-compliance with these standards, exposing project stakeholders to legal liabilities and penalties. Moreover, the lack of adherence to regulatory requirements undermines public trust in the construction industry and erodes confidence in the safety of built environments.
In the realm of construction, the adage "you get what you pay for" holds true perhaps more than in any other industry. While the allure of cost savings may be tempting, the consequences of using substandard materials far outweigh any short-term financial gains. From compromised safety and shortened lifespan to economic fallout and environmental consequences, the impact of subpar materials reverberates across multiple dimensions.
To ensure the longevity, safety, and integrity of construction projects, stakeholders must prioritize quality at every stage of the building process. Investing in reputable suppliers, adhering to stringent quality control measures, and upholding regulatory compliance are essential steps toward constructing a sustainable and resilient built environment for generations to come. In a world where the stakes are high and the repercussions are far-reaching, the choice between quality and compromise is clear: the foundation of our future depends on it.